In the ever-evolving world of additive manufacturing, Selective Laser Sintering (SLS) has emerged as a game-changer. This advanced 3D printing technology offers unparalleled precision, speed, and versatility, making it a preferred choice for various industries. But what exactly are selective laser sintering services, and how can they maximize efficiency in your operations?
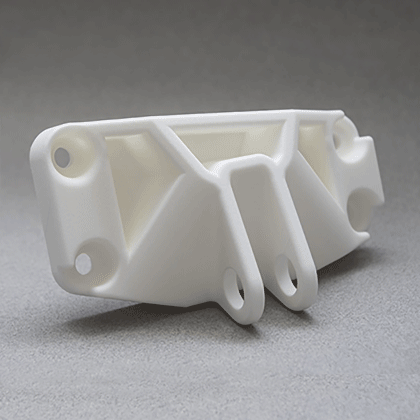
Understanding Selective Laser Sintering Services
Selective Laser Sintering (SLS) is a 3D printing technique that uses a high-powered laser to fuse small particles of polymer powder into a solid structure. Unlike other 3D printing methods, SLS does not require support structures, allowing for more complex geometries and intricate designs. This makes it ideal for producing functional prototypes, end-use parts, and even small production runs.
How Does SLS Work?
The SLS process begins with a digital 3D model, which is sliced into thin layers. The laser then selectively fuses the powder layer by layer, creating a solid object. The unfused powder acts as a support, eliminating the need for additional support structures. This results in less material waste and more efficient production.
Benefits of Selective Laser Sintering Services
Why should you consider SLS for your manufacturing needs? Here are some key benefits:
- High Precision: SLS can produce parts with intricate details and tight tolerances.
- Material Versatility: A wide range of materials, including nylon, glass-filled nylon, and flexible thermoplastics, can be used.
- Cost-Effective: Reduced material waste and the ability to produce complex parts without additional support structures make SLS a cost-effective option.
- Rapid Prototyping: SLS enables quick turnaround times, allowing for faster product development cycles.
Applications of Selective Laser Sintering Services
SLS is widely used across various industries due to its versatility and efficiency. Some common applications include:
- Aerospace: Lightweight, high-strength components for aircraft and spacecraft.
- Automotive: Functional prototypes and end-use parts for vehicles.
- Medical: Custom implants, prosthetics, and surgical instruments.
- Consumer Goods: Customized products, such as eyewear and footwear.
Choosing the Right SLS Service Provider
When selecting a provider for selective laser sintering services, consider the following factors:
- Experience: Look for a provider with a proven track record in SLS and a portfolio of successful projects.
- Material Options: Ensure the provider offers a variety of materials to meet your specific needs.
- Quality Assurance: Check for certifications and quality control measures to ensure high-quality output.
- Customer Support: A responsive and knowledgeable support team can make a significant difference in your experience.
“Selective Laser Sintering has revolutionized the way we approach manufacturing, offering unprecedented flexibility and efficiency.”
For instance, the XYZ SLS Printer offers exceptional precision and a wide range of material options, making it a top choice for many industries.
Additionally, you can watch this informative video to learn more about the capabilities of SLS technology.
Conclusion
Selective laser sintering services offer a powerful solution for modern manufacturing challenges. By leveraging the precision, versatility, and efficiency of SLS, businesses can streamline their production processes and bring innovative products to market faster. Whether you're in aerospace, automotive, medical, or consumer goods, SLS can help you achieve your manufacturing goals with ease.